Pros and Cons of Unique or Serial Barcoding Items in The Warehouse

In this era of online commerce, effective e-commerce warehouse management can sustain or impede an operation’s lifespan. As companies scale, the product flows intensify demanding precision in inventory tracking. This is where the barcoding system steps in as a powerful ally. By streamlining the process of identifying, locating, and managing items, barcoding technology allows businesses to minimize errors and optimize workflows.
Yet, within barcoding lies a critical decision: should businesses adopt item barcodes, where each identical product shares
the same code, or opt for serial barcodes, where each item is given a unique
identifier following a sequence? Each system brings distinct advantages and challenges to e-commerce warehouse management.
In this blog, we will understand each barcoding type, examine their impact on operations, and help you decide the best fit for your business.

Item vs. serial—which boosts your efficiency best?
Understanding Unique and Serial Barcoding Systems
Warehouse environments are increasingly complex, and e-commerce businesses often deal with high volumes of varied SKUs (Stock Keeping Units). Barcoding addresses these complexities by enabling fast, accurate identification of products, reducing manual errors, and ensuring smooth inventory processes. However, not all barcoding methods serve the same purpose. Batch or Item barcoding and serial barcoding each have different roles and applications, suited to various business needs.
- Batch / Item Barcodes: A unique WMS barcode system assigns the same barcode to all identical items, meaning every unit of a specific SKU shares the same code. This system is efficient for businesses managing bulk inventory where items are interchangeable, such as in cases of non-perishable goods or standard products with minimal variability.
- Serial Barcodes: In contrast, serial barcoding assigns each item a unique identifier, creating a record for each product. For items requiring distinct tracking, such as high-value goods, electronics, serial barcodes prove invaluable. Serial barcoding can capture each item's journey, from arrival at the warehouse to final delivery.
How Barcoding Works in Warehouse Inventory Management
Modern e-commerce warehouse management relies on barcoding as a fundamental part of its inventory control systems. But how does barcoding work within a warehouse environment?
Inventory Tracking
Barcoding transforms inventory tracking into a precise and systematic process. Each item in the warehouse is tagged with a SKU or serial warehouse barcode, enabling quick monitoring at any given moment. When an item moves from receiving to storage to picking, packing, and eventually to shipping, each step is recorded via barcode scans. This ensures fast movement of stock and a continuous trail of data for each item, providing invaluable insight into item location, stock levels, and movement patterns. For warehouses, the benefits of barcoding for inventory tracking are numerous. Enhanced visibility, faster response times to stock-outs, and accurate stock counts have become the new norm.
Data Collection
Data collection is the cornerstone of multichannel retail warehouse management and barcoding plays a crucial role in capturing this data. With each barcode scan, information such as item ID, location, and transaction type is instantly recorded. This data is then processed to keep records up-to-date, supporting various functions, from order fulfillment to restocking.
One of the advantages of automated data collection is that it reduces the risk of human error. In warehouses with complex inventories, even minor errors in data entry can lead to substantial disruptions. Barcoding minimizes these errors, ensuring data consistency and accuracy.
Integration with ERP Systems
What role does the best retail ERP software play in WMS barcode technology? As warehouses become more complex, managing inventory without a centralized system becomes increasingly difficult. This is where ERP systems step in, providing a robust infrastructure that connects barcoded items with the broader business functions of the organization.
Through ERP integration, data from barcode scans is automatically fed into a unified platform, where it can be analyzed and used across departments. ERP systems allow warehouse managers to monitor inventory in real-time, trigger automatic stock reorder points, and optimize resource allocation based on current stock levels. Additionally, ERP systems play a key role in automating the data collection process, minimizing the need for manual entries. By streamlining this flow of data, ERP solutions significantly improve operational efficiency and accuracy.
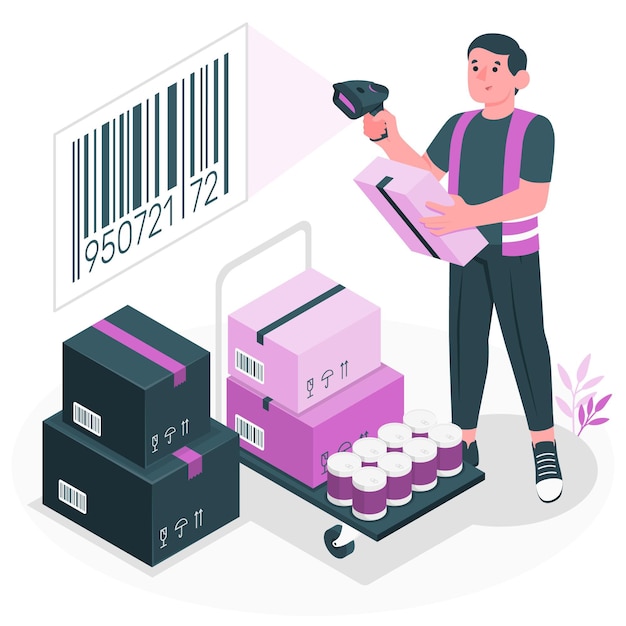
The Pros and Cons of Using Unique Barcodes in E-commerce Warehouse Management
SKU or Item barcodes have become an essential part of modern e-commerce warehouse management, streamlining everything from inventory control to order fulfillment. These days many brands are opting for serial barcoding even in low-cost items and fashion. Unique or Serial barcoding has become a powerful tool for modern e-commerce warehouse management, providing unique identifiers for each item. By assigning a unique barcode to each product, warehouses can achieve precise tracking and streamline various operations, from inventory management to order fulfillment. But like any technology, unique barcodes come with both advantages and challenges that warehouses must consider. Let’s break down the pros and cons of implementing unique barcodes in a busy e-commerce warehouse environment.
Pros | Cons |
---|---|
Improved Accuracy in Inventory Management: Unique barcodes ensure precise tracking for each item, reducing stock discrepancies and minimizing errors. This accuracy cuts down on time and costs associated with error correction, ultimately strengthening the business’s bottom line. | Increased Complexity and Cost: Implementing a unique or serial barcode system can be costly due to the necessary technology, training, and ongoing maintenance. Smaller operations may find these expenses challenging, potentially outweighing the system’s benefits. |
Streamlined Order Fulfillment: Unique barcodes enable fast and accurate picking and packing, accelerating order fulfillment and ensuring the correct products reach customers. This process improvement increases operational efficiency and customer satisfaction. | Potential for Data Overload: Each unique piece of item in the warehouse generates data with every scan, leading to vast information accumulation. Without effective data management, this can result in data overload, slowing processes, and decreasing operational efficiency. |
Enhanced Warehouse Operations: Unique barcoding supports detailed tracking of each item’s location, movement, and status, making it easier to manage returns, monitor shelf life, and conduct audits. This level of tracking minimizes bottlenecks and optimizes resource allocation. | Individual Scanning Requirement: Every item must be scanned individually during inbound and outbound processing. For high-volume warehouses, this requirement can be labor-intensive and time-consuming, with a risk of inaccuracies if items are missed or scanned incorrectly. |
Improved Customer Satisfaction: Serial barcoding helps ensure order accuracy and speeds up item location, boosting customer satisfaction. Reduced errors build trust in the brand, especially vital in e-commerce. | Risk of Delays Due to Mismatched Codes: Unique identifiers increase the risk of shipment delays from mismatched codes. Minor discrepancies require manual intervention to resolve, which can hinder efficiency in time-sensitive operations, especially if items with similar appearances have different barcodes. |
Integration issues with Websites, OMS and ERP Unique or serial codes have a disadvantage that all data exchange with other systems have to be summed up for item level information exchange. This leads to complex coding requirements at the data producer and consumer end. |
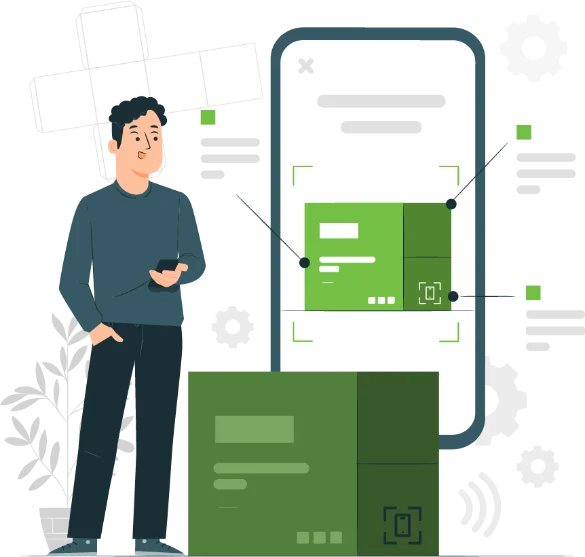
Master inventory precision: Item vs. serial barcoding
Comparison: Unique vs. Serial Barcoding for E-commerce Warehouse Management
When managing an e-commerce warehouse, the choice between unique and serial barcoding can significantly impact inventory accuracy, traceability, and overall efficiency. Here’s a closer look at how these two barcoding systems compare and the unique advantages each offers:
Feature | Item or SKU Barcodes | Unique or Serial Barcodes |
---|---|---|
Simplicity | Simple to implement and manage. | More complex due to individualized tracking. |
Traceability | This WMS barcode technology provides no traceability for individual pieces. | High traceability, each item has a unique identifier. |
Cost | Lower implementation and operational costs. | Higher costs due to the need for additional data handling. |
Data Management | Lesser data to store and manage. | Potential data overload with large inventory volumes. |
Warehouse Operations Impact | Easier for single channel inventory management. | Supports advanced inventory processes, may need more training. |
Decision Factors | Ideal for high-volume, low-value items. | Suitable for unique, high-value, or regulated products. |
Best for | Low-cost items or items where individual tracking is not needed. | This WMS barcode technology provides high-value or regulated items requiring detailed tracking. |

Best Practices by Ginesys for Implementing Barcode Systems in E-commerce Warehouses
As the best retail ERP software, Ginesys offers a suite of advanced tools tailored to the needs of e-commerce warehouse management. With proven expertise in warehouse automation, the platform has developed best practices for implementing barcode systems that enhance efficiency, accuracy, and cost-effectiveness. Here’s how Ginesys can transform barcode implementation for the warehouse.
- Integration with ERP and Warehouse Management Systems (WMS): Integrating barcoding systems directly with ERP and WMS solutions is critical for real-time inventory tracking and data accuracy. Ginesys system, generate item codes as well as serial codes, pushes to WMS and ERP and thus enables seamless integration between these modules, ensuring data consistency across all systems. This connectivity helps automate stock updates and minimizes the chance of human error, leading to precise inventory records.
- Choosing the Right Barcode Technology: Is a one-dimensional (1D) barcode sufficient, or does the warehouse require a two-dimensional (2D) or QR code system for higher data capacity? Ginesys emphasizes selecting WMS barcode technology that aligns with a warehouse’s unique requirements, ensuring compatibility with scanning equipment, inventory size, and operational speed. Choosing the correct barcode technology helps streamline inventory management and future-proof the system as warehouse needs evolves.
- Staff Training and Warehouse Automation: Efficient warehouse operations depend on skilled staff. Ginesys advocates for thorough training programs to familiarize staff with barcode scanning, handling, and troubleshooting, empowering employees to leverage WMS barcode technology effectively. Alongside training, the platform encourages automation where possible, reducing manual tasks and improving operational efficiency. Automation minimizes human error, reduces reliance on manual labor, and accelerates warehouse processes.
- Optimizing Placement of Barcodes: Barcode placement may seem trivial but can impact scanning speed and efficiency. Placing barcodes on accessible areas of products or packaging ensures faster, error-free scanning. Ginesys provides guidelines for optimal barcode placement based on the product type, packaging, and storage method, promoting faster and more reliable scanning processes throughout the warehouse.
- Automated Reconciliation of Barcodes and Inventory: Inventory discrepancies can disrupt e-commerce warehouse management and lead to inaccurate reporting. It recommends implementing automated reconciliation practices to regularly verify barcode data against physical inventory. This practice helps identify and correct mismatches promptly, ensuring the inventory count remains accurate and up to date.
How Ginesys Leverages Barcoding for Efficient Warehouse Management
Ginesys has established itself as the best retail ERP software with a comprehensive suite of tools for e-commerce and retail businesses. From inventory management to warehouse automation, it offers solutions that streamline operations, reduce errors, and enhance overall efficiency. Leveraging their advanced ERP and WMS capabilities, warehouses can optimize barcoding systems, ensuring smooth operations even in high-demand periods. By adopting best practices and leveraging Ginesys' expertise, warehouses can achieve a balance between speed, accuracy, and cost-effectiveness in barcode management.
The platforms offer a comprehensive suite tailored to the demands of e-commerce. Its innovative approach to barcoding transforms e-commerce warehouse management, ensuring that inventory moves efficiently from shelf to shipment. How does Ginesys achieve this?

Revolutionize warehouse efficiency with Ginesys barcode solutions
Unique Features of Ginesys in Handling Serial and Unique Barcoding
Ginesys provides both item-wise and serial barcoding systems, each designed to cater to specific operational needs. Unique or Serial barcoding, where each item has a distinct barcoding in warehouse, enables highly detailed tracking of individual products, which proves invaluable for industries where traceability and regulatory compliance are paramount. Item or SKU barcoding, in contrast, assigns a single barcode to multiple identical products. This approach is particularly beneficial for managing bulk items and streamlining processes, as it reduces the scanning time for identical items.
The advanced features of Ginesys allow businesses to implement these barcoding techniques with ease. For instance, the system’s adaptability means that warehouses can handle both unique and serial barcode scanning in Warehouse Management System, catering to mixed inventory models where some products require item-specific tracking while others benefit from batch-level management.
Benefits of Integrating Ginesys with Unique Barcoding for Real-Time Inventory Tracking and Order Fulfillment
Integrating Ginesys with unique barcoding opens a seamless, real-time approach to managing inventory and fulfilling orders, enabling greater accuracy and operational efficiency. With unique barcodes, each product is assigned an identifier that distinguishes it from others, reducing misplacement and ensuring precise stock counts. Here’s how it can transform the inventory management:
- Enhanced Tracking Accuracy: A unique barcode scanner in warehouse allows for precise tracking at every stage, from receiving to shipping. This ensures inventory levels are always up to date, reducing the risk of stockouts or overstocking.
- Efficient Order Fulfillment: With accurate, real-time inventory data, fulfilling orders becomes faster and error-free. Unique barcodes help staff locate items quickly, reducing fulfillment times and improving customer satisfaction.
- Streamlined Warehouse Operations: Combined with unique barcoding, it minimizes manual data entry, which can lead to errors and inefficiencies. This integration supports seamless inventory updates, creating a streamlined workflow that enhances productivity.
- Reduced Shrinkage and Loss: Unique barcode scanner in warehouse minimize the chances of misplaced or lost items, helping companies reduce inventory shrinkage. With Ginesys, these barcodes also make it easier to track product returns accurately.
- Better Data Insights: By capturing detailed, real-time data on inventory movement, businesses can leverage insights for smarter decision-making around inventory levels, reorder points, and demand forecasting.

Transform your warehouse efficiency with Ginesys barcode best practices!
Final Thoughts
Both item and serial barcoding present distinct advantages for e-commerce warehouse management. However, each method comes with challenges—unique barcoding can be resource-intensive, while item barcoding might fall short in high-traceability scenarios.
To navigate these complexities, e-commerce businesses may find solutions like Ginesys invaluable. By offering a flexible, integrated barcoding, WMS and ERP approach to barcoding, it powers warehouses with the technology to streamline operations, improve accuracy, and enhance customer satisfaction. For those looking to elevate their e-commerce warehouse management, exploring the robust offerings of ERP software like Ginesys could be the next step toward achieving seamless and efficient e-commerce operations.
Elevate accuracy, streamline operations, and enhance customer satisfaction—explore Ginesys today for a smarter, more efficient e-commerce future.